5TPD Batch Soybean Oil Refining Line in Ghana
The Ghanaian customer already operates a 25TPD soybean oil pressing plant, which consists of essential equipment including 1PC Cleaning Sieve, 1PC Steam Cooker, 1PC Crusher, 3PC Oil Presses, and 1PC Oil Filter. This setup enables the efficient extraction of crude soybean oil, catering to local demand. However, to further improve the quality of the oil and meet more stringent market requirements, the customer decided to install a 5-ton-per-day batch soybean oil refining line.
5 TPD Batch Soybean Oil Refinery in Ghana
The newly planned refinery will focus on refining crude soybean oil into a higher-quality product. The process chosen for this setup is chemical refining, which is particularly effective for removing free fatty acids and other impurities from the oil. The core steps of the refining process include: neutralization, water washing, decoloration, filtering and deodorization.
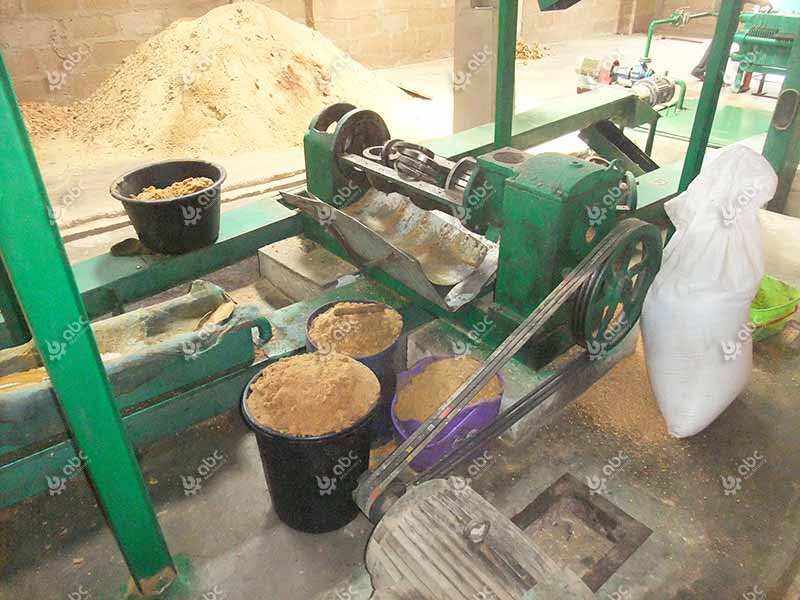
Soybean Oil Pressing Site in Ghana
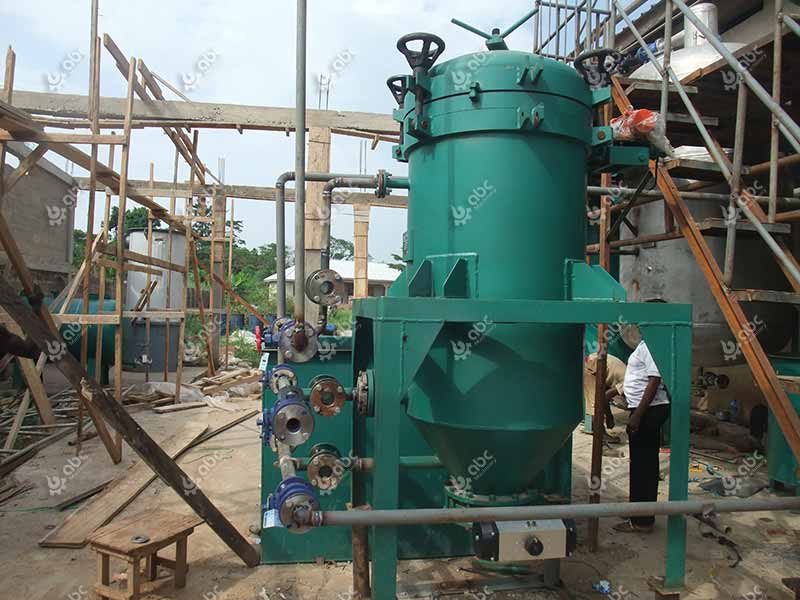
Soybean Oil Filter in Ghana
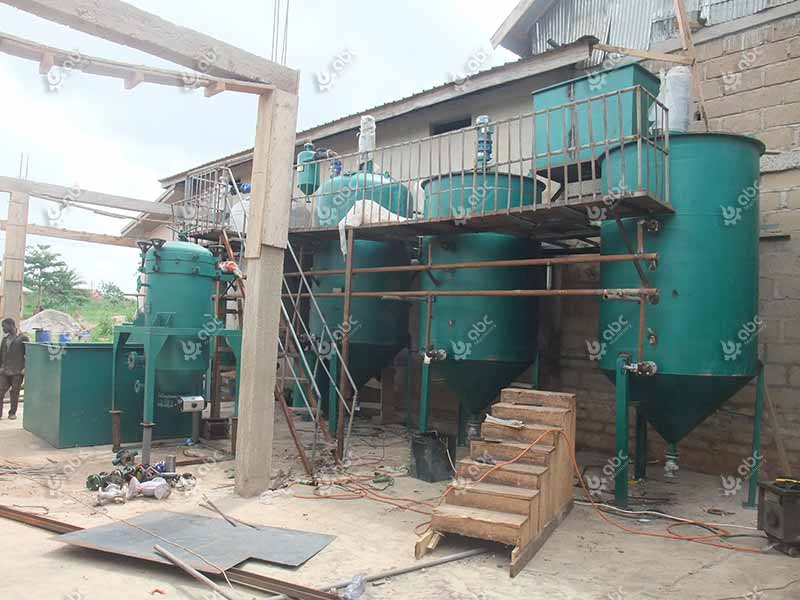
Welding Heat Transfer Oil Pipeline in Soybean Oil Refinery
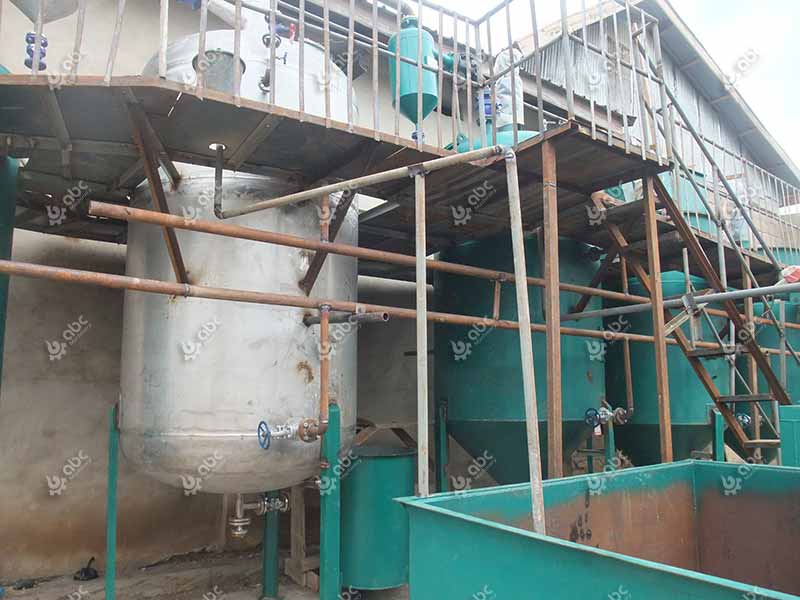
Connecting Pipeline of the Decolorized Oil Refining Tank
Key Considerations for Setting Up a 5TPD Soybean Oil Refinery in Ghana
The customer in Ghana currently operates a 25-ton/day soybean oil extraction line. To enhance the quality of their oil, they are moving forward with the installation of a 5-ton/day batch soybean oil refining line. Below are several important aspects to consider during the construction of the plant:
-
Neutralization Section: This phase is essential for removing free fatty acids from the crude oil. Alkali, such as caustic soda, is used in the process to neutralize the acids and form soap stock, which is then separated from the oil. To ensure durability, it's important to use corrosion-resistant materials for the neutralization tank. Moreover, the precise control of alkali dosage is key to preventing over- or under-neutralization, both of which could affect the quality of the final product and lead to oil losses.
-
Water Washing Section: After neutralization, the oil undergoes a water washing process to remove any soap and residual impurities. Effective water management is crucial in this stage. The system should be designed for efficient drainage and reduced water and energy consumption. Additionally, using clean, high-quality water that is regularly monitored will help ensure the oil is thoroughly purified.
-
Decolorization Section: The decolorization process uses bleaching earth or activated clay to remove unwanted pigments from the oil. Automated controls should be implemented to precisely manage temperature and duration during this process, optimizing the removal of color bodies. Ensuring that the decolorization equipment is appropriately sized for the refinery’s production capacity is also important for maintaining operational efficiency.
-
Filtering Section: Following decolorization, the oil needs to be filtered to remove any remaining particles or impurities. Selecting filters with the right precision and capacity is vital for maintaining high efficiency while also extending the life of the filtration equipment. It is equally important to design the system with easy maintenance in mind, facilitating quick and efficient filter cleaning or replacement.
-
Deodorization Section: The final step is deodorization, where the oil is heated under vacuum to remove unwanted odors. For effective deodorization, the vacuum pump must maintain the necessary vacuum levels throughout the process. Additionally, it’s important to use an energy-efficient heating system to avoid overheating the oil, which could otherwise affect its quality.
In constructing the 5TPD soybean oil refinery, each step—whether it be equipment selection, layout planning, or managing temperature and time during processing—will have a significant impact on the refining process and final product quality. Thoughtful planning and attention to detail will help ensure the refinery meets both market demands and the customer's operational goals.